QR Code
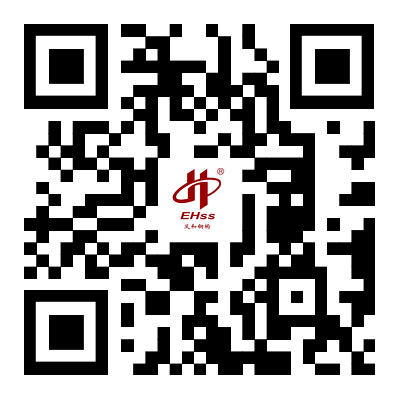
Prodotti
- Edificio a telaio in acciaio
- Magazzino della struttura in acciaio
- Edificio scolastico in acciaio
- Edificio in acciaio dell'ospedale
- Struttura in acciaio della stazione ferroviaria
- Struttura in acciaio dell'aeroporto
- Stadio con struttura in acciaio
- Sala espositiva con struttura in acciaio
- Case container
- Case prefabbricate
Contattaci
Telefono
E-mail
Indirizzo
N. 568, Yanqing First Class Road, Jimo High-Tech Zone, Qingdao City, Provincia di Shandong, Cina